Diagrams Mining Mill In The Cement Factory
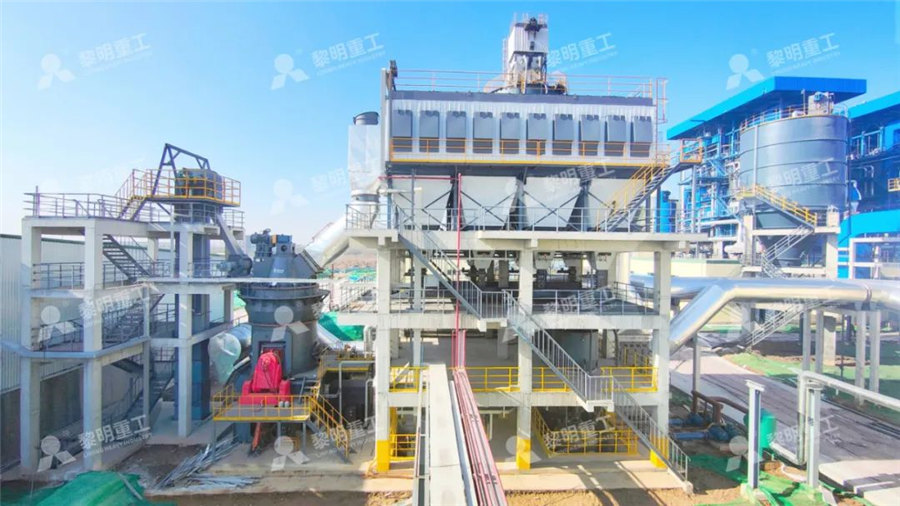
Cement Plant: The Manufacturing Process 4 5 World
2019年10月23日 together in a raw mill to a particle size of 90 micrometres, producing “kiln feed” Cement Plant: The Manufacturing Process worldcementassociation 1 Limestone (CaCO3) 2019年4月30日 The Cement Plant Operations Handbook is a concise, practical guide to cement manufacturing and is the standard reference used by plant operations personnel worldwide The Cement Plant Operations Handbook International 3 天之前 The cement manufacturing process starts from the mining of raw materials that are used in cement manufacturing, mainly limestone and clays A limestone quarry is inside the Manufacturing process Lafarge2024年2月11日 From the limestone quarry and cement mining process to the delivery of the product, you must follow each cement manufacturing step The raw materials for cement manufacturing are limestone (calcium), sand clay All Stages of Cement Manufacturing from The
.jpg)
Manufacturing process flow 1 Quarrying and Crushing
2019年7月20日 9 Cement Grinding A closed circuit grinding system is applied The main equipment consists of a 46x12m double compartment tube mill and a sepax separator This 2019年7月20日 The whole process of cement manufacturing in Messebo Cement plant which consists of two separate Cement Production lines can be summarized into the following CEMENT PRODUCTION AND QUALITY CONTROL2024年7月29日 According to [39], Figure 4 provides a process flow diagram of the general cement production process and the associated inputs, during various steps of the production Process flow diagram for the cement manufacturing process, Download scientific diagram Schematic layout of a typical allintegrated cement manufacturing process Red dashed lines depict confined spaces The process commences with raw Schematic layout of a typical allintegrated cement
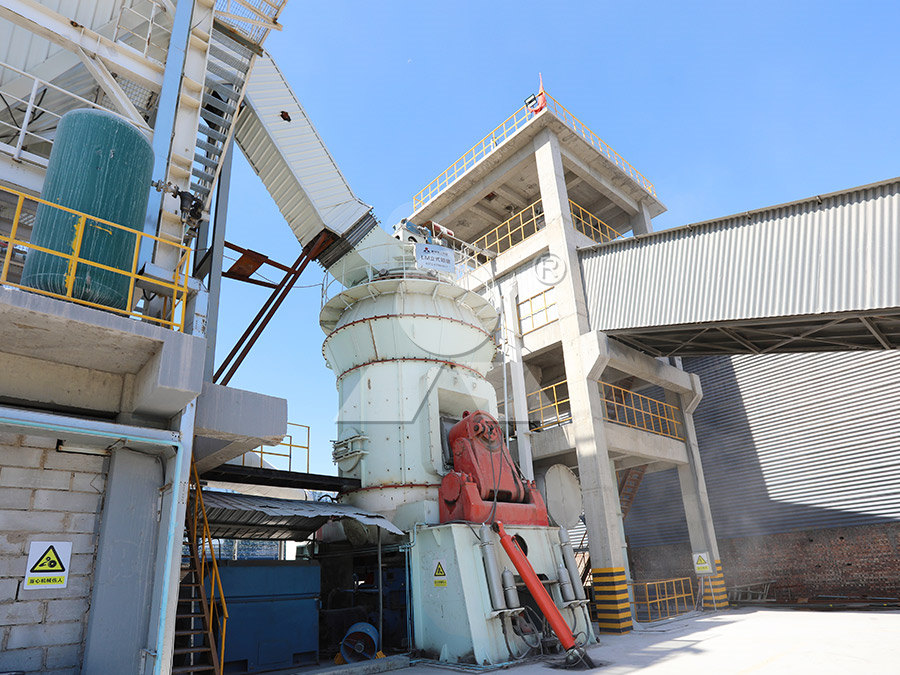
Mining Activities, Cement Production Process and Quality
2022年7月4日 There are two open pit mines, namely Livwezi and Chikoa, at Shayona Cement factory in Kasungu They conduct all mining activities including drilling, blasting and hauling 2019年4月30日 Finish mill – 12 Cement – 13 Quality control – 14 Packing and distribution – 15 Emission abatement (dust, NO x, SO 2, etc) – 16 Maintenance – 17 Process – 18 Materials analysis –19 Plant capacity summary – 20 Storage capacity 15 Cement plant construction and valuation 244 1 New plant construction – 2The Cement Plant Operations Handbook International 2024年9月26日 Cement Extraction, Processing, Manufacturing: Raw materials employed in the manufacture of cement are extracted by quarrying in the case of hard rocks such as limestones, slates, and some shales, with the aid of blasting when necessary Some deposits are mined by underground methods Softer rocks such as chalk and clay can be dug directly by excavators Cement Extraction, Processing, Manufacturing BritannicaClimate change has become a prominent global issue due to human activities One of the major green house gas emitting sources (CO2) to the environment are considered as flue gases, which generated Typical cement manufacturing process flow diagram [4]
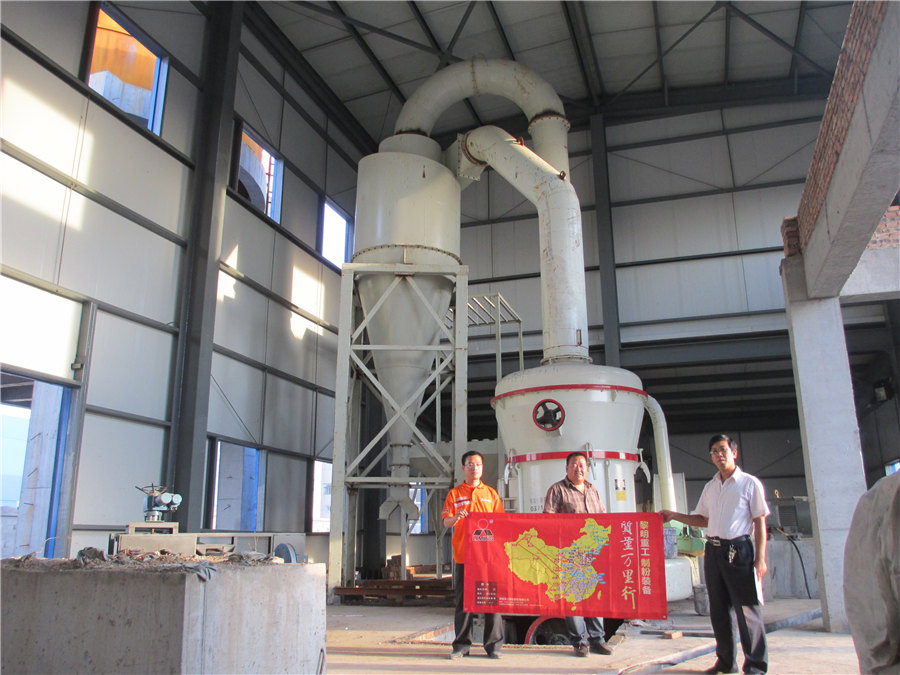
Manufacturing process Lafarge
3 天之前 The raw mill contains two chambers, separated by diaphragm, namely a drying chamber and a grinding chamber The hot gases coming from a preheater (preheater / kiln system) enter the mill and are used in raw mills for drying Then the drying materials enter the grinding chamber of raw mills for fine grinding2022年7月4日 Figure 28: Showing the raw mill at stationary, Shayona cement factory The raw mill has capac ity of 50 tons per hour and takes 300KW of electricity The mill’s mainMining Activities, Cement Production Process and Quality 2021年4月27日 %PDF16 %âãÏÓ 83 0 obj > endobj 102 0 obj >/Filter/FlateDecode/ID[99BDAE142B8D9E49ED83701F0>]/Index[83 28]/Info 82 0 R/Length 96/Prev /Root 84 0 R Mining Engineering Consultants PEC Consulting Group2024年10月22日 Stage of Cement Manufacture There are six main stages of the cement manufacturing process Stage 1: Raw Material Extraction/Quarry The raw cement ingredients needed for cement production are limestone (calcium), sand and clay (silicon, aluminum, iron), shale, fly ash, mill scale, and bauxite The ore rocks are quarried and crushed into smaller How Cement is Made Cement Manufacturing Process
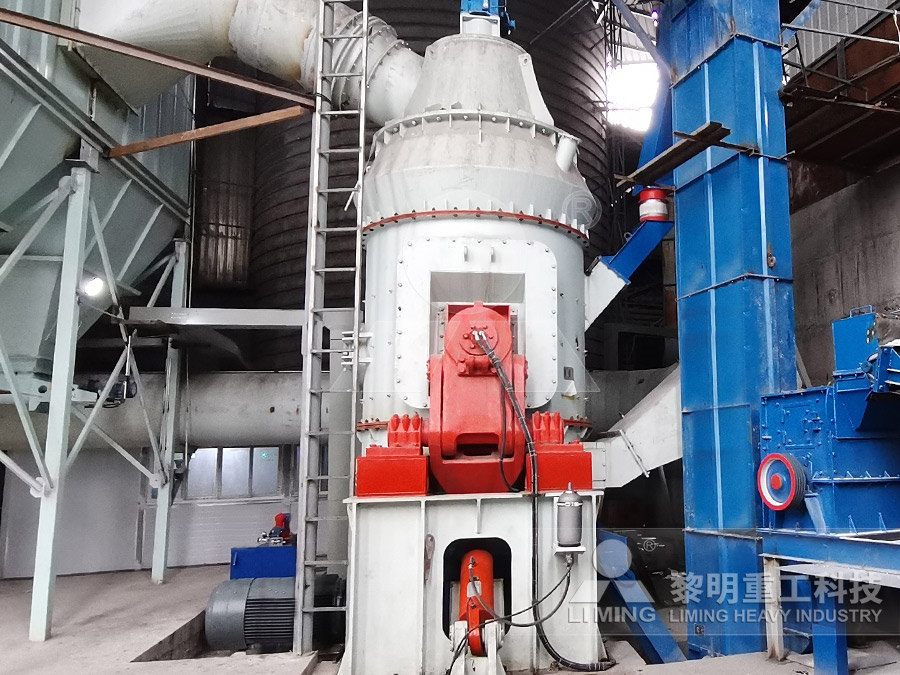
Cement Plant: The Manufacturing Process 4 5 World
2019年10月23日 The cement is then packed and distributed to consumers The kiln feed is blasted in a cement kiln at a temperature of 1450oC, causing clinkering to occur (small balls of up to 25mm diameter) 6 5 Raw mill Preheated tower Cement storage silos Packing warehouse Raw material silos Limestone storage and preblending unit Rotary Kiln Additives Silos 2018年10月10日 The grid diagram shown in Figure 8 is the base concept of a new heat exchanger network of a cement factory with minimized energy consumption It has additionally installed four heat exchangers with an estimated heat transfer area of 15551 m 2 and total recovered heat energy of 579008 kWHeat Integration in a Cement Production IntechOpen2 天之前 As the perflow diagram of the wet process of cement manufacturing, the rotary kiln is an essential and important component of a cement manufacturing factory 6 It is made of a thick steel cylinder of diameter anything from 3 meters to 8 meters, lined with refractory materials, mounted on roller bearings, and capable of rotating about its axis Wet Process Of Cement Manufacturing With Flow Chart2 天之前 As the perflow diagram of the wet process of cement manufacturing, the rotary kiln is an essential and important component of a cement manufacturing factory 6 It is made of a thick steel cylinder of diameter anything from 3 meters to 8 meters, lined with refractory materials, mounted on roller bearings, and capable of rotating about its axis Wet Process Of Cement Manufacturing With Flow Chart
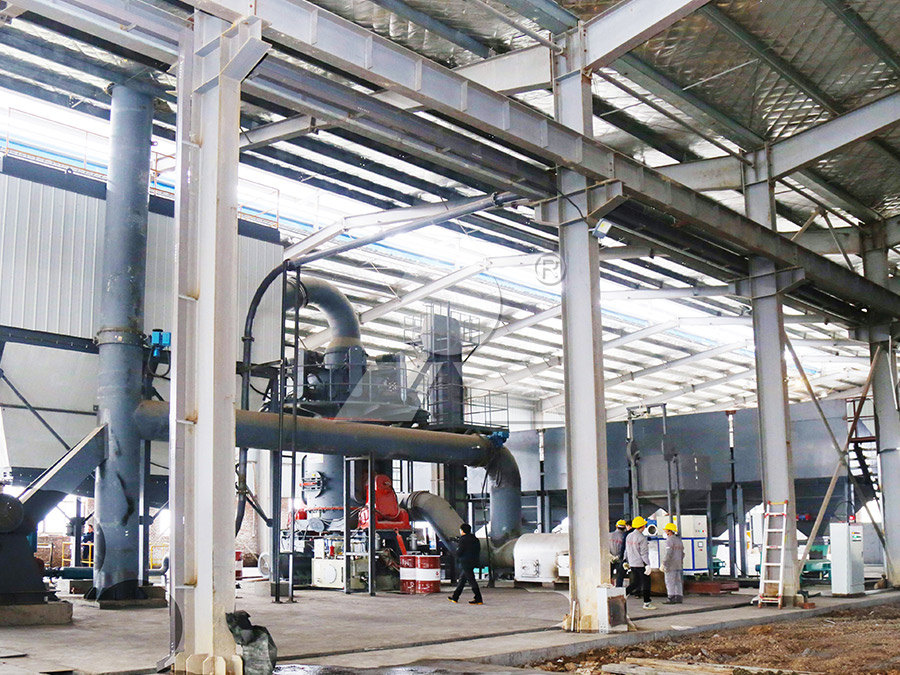
Cement Mill Process Requirement of Mill Motors Kiln
Every stage has its own drive Several drives in Cement Mill Process are raw mill drives, cement mill drives, kiln drives, crusher drives, waste gas fan drives and compressor drives Requirement of Mill Motors: They should have high starting torque The starting current must be limited to a maximum of two times full load value to minimise 2015年1月12日 The document discusses the Indian cement industry It notes that cement is used for construction purposes like buildings, transport infrastructure, and water systems The main raw materials used are limestone, Cement industry PPT SlideShare2023年3月27日 The cost of setting up a cement factory in Nigeria will depend on several factors, such as the location, size, and type of cement plant The cost can also vary based on the availability of raw The cost of setting up a cement factory in Nigeria LinkedInCement Industry: Ball mills are extensively used in the cement industry for grinding raw materials, clinker, and additives to produce cement and recent developments helps to appreciate their significance and wideranging applications in industries such as cement, mining, pharmaceuticals, chemicals, ceramics, and more Factory Show Ball Mill Grinding Machines: Working Principle, Types, Parts
.jpg)
Cement Manufacturing Process and Its Environmental Impact
2023年7月10日 Cement manufacturing is a significant industrial activity that plays a vital role in the construction sector However, the process of cement production is associated with various environmental The higher amount of energy consumption is due to the lack of work efficiencies tools leading the waste heat [13] They found that about 40% of the total input energy was lost through kiln shell Process Flow Diagram of the Cement Plant ResearchGate2024年7月29日 Sustainable cement production can be achieved by full or partial replacement for cement with natural occurring material such as kaolin, clay, silica sand and pumice (Chaudhary et al, 2015;Yu et Process flow diagram for the cement manufacturing process, 2021年2月8日 Deep decarbonisation of industry: The cement sector Cement sector overview Cement is the binding agent of concrete, the most widely used construction material in the world The cement sector is a major greenhouse gas emitter, responsible for about 7% of CO 2 emissions globally (1), and about 4% in the EUDeep decarbonisation of industry: The cement sector
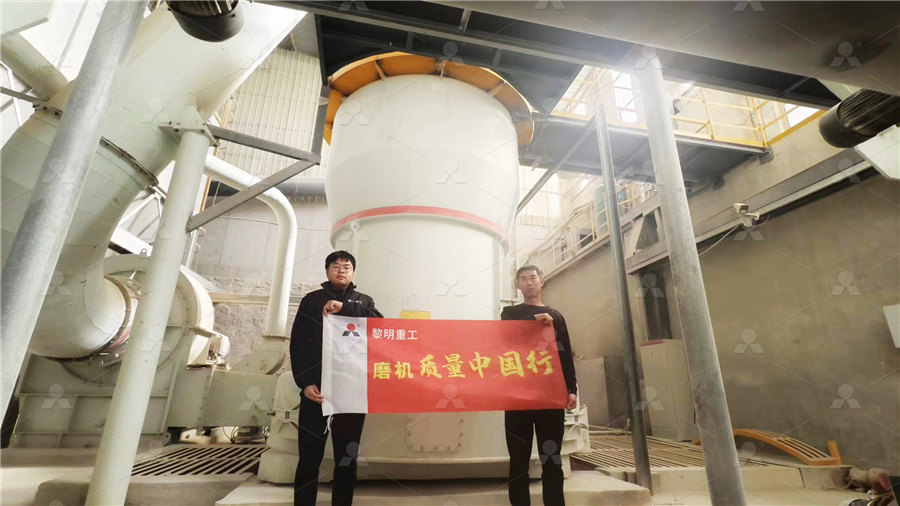
(PDF) Grinding in Ball Mills: Modeling and Process Control
2012年6月1日 As the cylinder starts to rotate, the grinding balls inside the cylinder crush and grind the feed material, generating mechanical energy that aids in breaking bonds, activating the catalyst, and What Is A Cement Ball Mill The cement ball mill is a kind of cement grinding millIt is mainly used for grinding the clinker and raw materials of the cement plant, and also for grinding various ores in metallurgical, chemical, and electric Cement Ball Mill Cement Grinding MachineThe higher amount of energy consumption is due to the lack of work efficiencies tools leading the waste heat [13] They found that about 40% of the total input energy was lost through kiln shell Process Flow Diagram of the Cement Plant ResearchGate2023年12月20日 The clinker is ground to a fine powder in a cement mill and mixed with gypsum to create cement The complex process of making cement starts with the mining of raw materials like limestone and clay, which are then The Cement Manufacturing Process Thermo
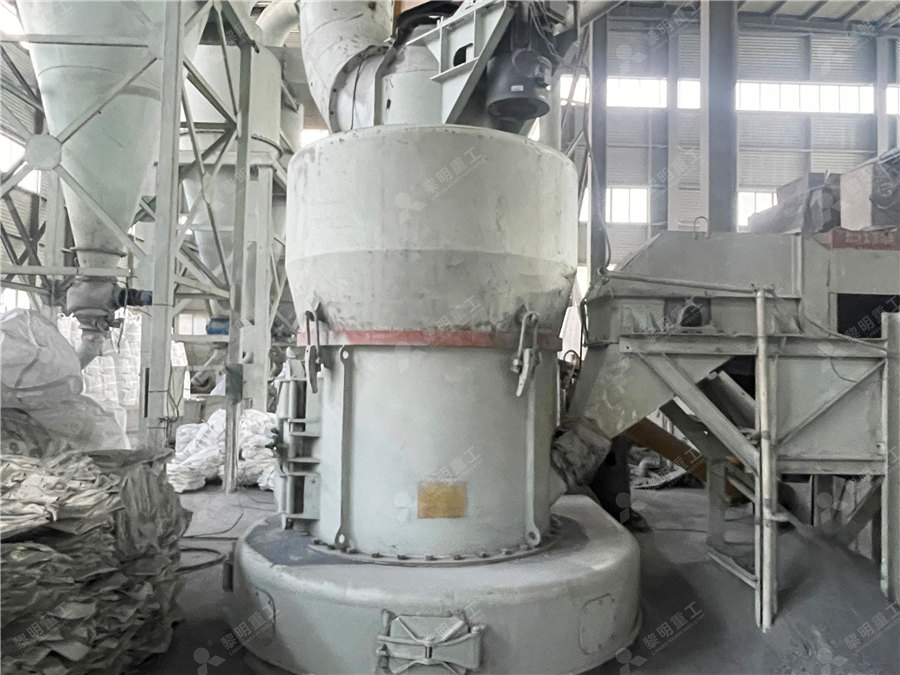
Microsoft Word GHG BACT paper for Cement October
2021年6月25日 III Description of the Cement Manufacturing Process Cement is a finely ground powder which, when mixed with water, forms a hardening paste of calcium silicate hydrates and calcium aluminate hydrates Cement is used in mortar (to bind together bricks or stones) and concrete (bulk rocklike building material made from cement,Download scientific diagram 4000 Tonne cement factory in Myaing Kalay, Hpaan The cement factory was built since 1980 and developed as 900 tons Myaing Kalay Cement Factory Four thousand tons of 4000 Tonne cement factory in Myaing Kalay, Hpaan The cement factory 2024年4月24日 clinker are processed in the mill, divided into two stages: the grinding stage in chamber I and the milling stage in chamber II In the final stage, the cement is transferred to the separation stage, where the raw material is returned to the mill while the fine cement is stored in the storage silo [38, 40] 23 Cement Packaging and DispatchImpacts of Cement Production on the Environment with 2012年4月30日 The objective of this article is the development of a novel raw material mix proportion control algorithm for a cement plant raw mill, so as to maintain preset target mix proportion at the raw (PDF) Process Automation of Cement Plant ResearchGate
.jpg)
Distribution of dust emissions at bag filters in the cement mill
Download scientific diagram Distribution of dust emissions at bag filters in the cement mill section no1 (mill filterpoint A and separator filterpoint B, Figure 1) of the analyzed cement plant 2023年3月27日 The cost of setting up a cement factory in Nigeria will depend on several factors, such as the location, size, and type of cement plant The cost can also vary based on the availability of raw The cost of setting up a cement factory in Nigeria LinkedIn2023年10月29日 The cement industry is a major contributor to carbon emissions, responsible for 5–8% of global emissions This industry is expanding, particularly in emerging economies, and it is expected that CO2 emissions will rise by 4% by 2050 To address this critical concern, this paper identifies ten factors that contribute to carbon emissions in the cement production Evaluation of Carbon Emission Factors in the Cement Download scientific diagram The scheme of the area where the cement factory is with a rotary cement kiln with clinker: 1 branch fan A; 2 branch fan B; 3 heat exchanger; 4 rotary cement kiln The scheme of the area where the cement
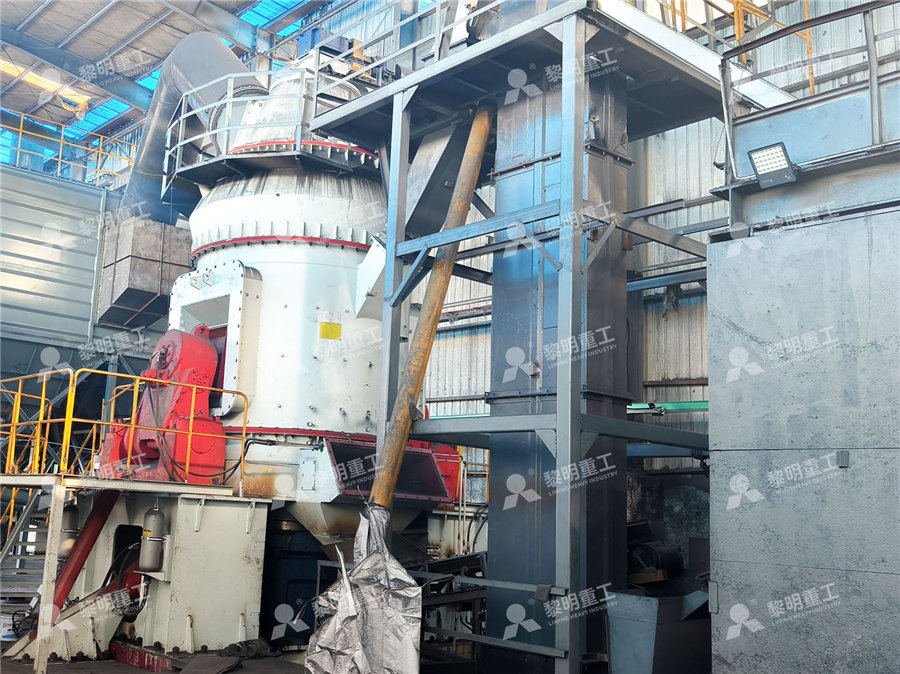
All Stages of Cement Manufacturing from The
2024年2月11日 A cement manufacturing facility is an extension of a cement mining sand clay (silicon, aluminum, iron), shale, fly ash, mill scale bauxite The ore rocks are quarried and crushed into little parts of about 6" series" Concrete is essential for upgrading American infrastructure and maintaining our built environment as we know it Partner of the Year PCA is proud to be a US Environmental Protection Agency’s (EPA) ENERGY STAR Partner of the Year Portland Cement AssociationThe manufacturing of Portland cement is the most common type of cement formation which is used in the construction sector It is a type of hydraulic cement invented by Joseph Aspdin of England in 1824 It was produced from a mixture of limestone and clay It got its name due to its high resemblance to the Portland stone in EnglandUnderstanding the Manufacturing Process of Cement and its In the diagram above of a precalciner kiln, raw meal passes down the preheater tower while hot gases rise up, heating the raw meal At 'A,' the raw meal largely decarbonates; at 'B,' the temperature is 1000 C 1200 C and intermediate compounds are forming and at 'C,' the burning zone, clinker nodules and the final clinker minerals formThe cement kiln Understanding Cement
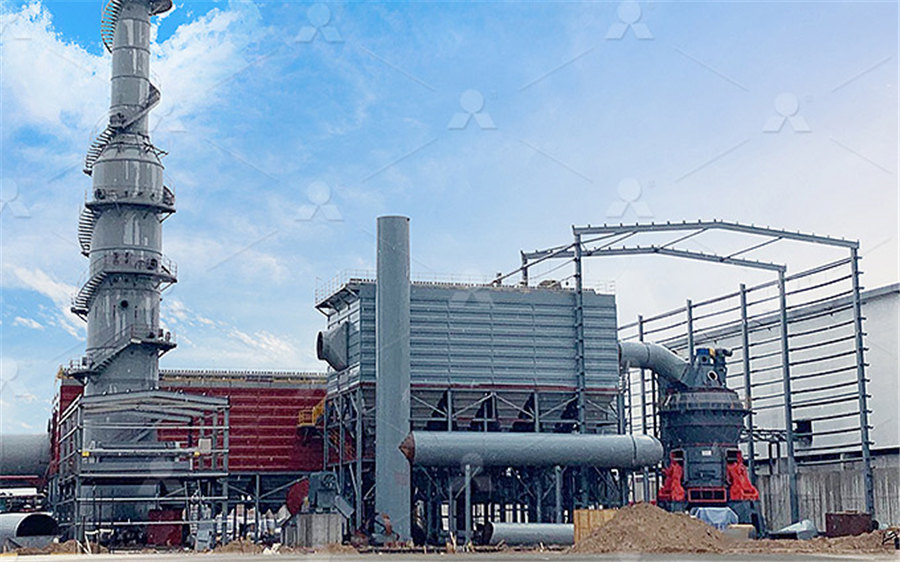
A practical guide to improving cement manufacturing
2024年5月22日 Cement manufacturing is the source of 5% of global CO 2 emissions 60% of emissions are due to the transformation of raw materials at high temperatures and 40% results from the combustion required to heat the cement kilns 1400°C to1500°C Therefore emissions monitoring is extremely critical for cement plants to meet regulatory requirements2019年7月31日 The cement industry is one of the most important primary industries in constructing and developing infrastructures that produce concrete and building materials(PDF) Environmental Pollution by Cement IndustryThree stations were chosen for each company (raw materials grinding mills, cement grinding mills and exhaust fan stations) having different electrical motor capacitiesFigure1: Schematic diagram of process units in a cement factoryJoin ResearchGate to access over 30 million figures and 160+ million publications – all in one placeCEMENT MANUFACTURING PROCESS FLOW CHART Download Scientific Diagram
.jpg)
Mastering Process Control Instrumentation in Cement Plants:
2023年9月5日 Pressure sensors used in the grinding mills and the separators need to be highly accurate, as even a small variation in the pressure can affect the efficiency of the grinding process and the quality of the cement In cement plants, bulk material level measurements are crucial for efficient and safe operations